|
Post by davidsyj on Feb 8, 2013 15:36:59 GMT -6
Thanks to Jeffrey Lane (if that's who he really is) I purchased my rear diff cover for my 8.8 through Clyde at Spyder Offroad. He ordered it for me and had it shipped to my door (well, was supposed to but he gave them his address instead  ) The material is nice and thick, I think it's 1/4" on the ring and 3/8" on the plates. Mine came in 5 pieces and has to be welded together. The pieces seem to fit together pretty good, I've only tacked it in place so far. If anyone is interested in these covers I'd say go ahead and get with Clyde and order one for your rig. Once it's all together I know I'm going to be extremely satisfied with it.  NO!!! Nothing in this picture is for sale!!! 
|
|
|
Post by Somebody on Feb 8, 2013 22:27:26 GMT -6
Picture??? What picture??
FAIL!!!!
|
|
|
Post by davidsyj on Feb 10, 2013 10:07:31 GMT -6
Picture??? What picture?? FAIL!!!! Fixed. It's there now. I don't know what happend with that.
|
|
Greg
Full Member
 
Posts: 330
|
Post by Greg on Feb 10, 2013 11:04:28 GMT -6
Looks beefy, think I'm going to have to pick up a couple.
|
|
|
Post by davidsyj on Feb 10, 2013 11:18:09 GMT -6
Looks beefy, think I'm going to have to pick up a couple. I was surprised at the thickness of the material. Plus for $60.00 you cant go wrong.
|
|
|
Post by Weezul on Feb 10, 2013 11:33:48 GMT -6
Any warping of the main ring?
|
|
|
Post by James on Feb 10, 2013 12:18:00 GMT -6
It hasn't been fully welded yet has it? That's when you have to worry about warping. It really needs to be bolted on when final welding is done.
|
|
|
Post by slinky on Feb 10, 2013 12:22:58 GMT -6
It hasn't been fully welded yet has it? That's when you have to worry about warping. It really needs to be bolted on when final welding is done. ^^^^^^^ This or at least bolt it to the tables in several spots to keep everything nice and flat then weld in small sections on opposite sides of the cover to keep the heat down on the metal.
|
|
|
Post by Weezul on Feb 10, 2013 12:45:07 GMT -6
That happened to me on the tabs I had to add on my bumper for the radiator hoop. Not a huge issue on a bumper but could lead to a lot of headache on a diff cover.
|
|
|
Post by mike on Feb 10, 2013 12:54:47 GMT -6
It hasn't been fully welded yet has it? That's when you have to worry about warping. It really needs to be bolted on when final welding is done. ^^^^^^^ This or at least bolt it to the tables in several spots to keep everything nice and flat then weld in small sections on opposite sides of the cover to keep the heat down on the metal. I agree with Dave that this is probably going to be the best way.
|
|
|
Post by davidsyj on Feb 10, 2013 13:04:17 GMT -6
I'm gonna bolt it to the axle for the final weld. That way it won't warp at all. I need to make sure of that because I will be installing my lube locker when this cover goes on.
|
|
|
Post by BEN on Feb 10, 2013 17:10:08 GMT -6
Well what ya waiting on? Looks good tho.
|
|
|
Post by jeffreylane on Feb 12, 2013 18:15:02 GMT -6
I think these are a great deal. I went with btf because they are about the only one who makes a real beefy 9.5 cover. It's real nice to have a fill plug now as well, since my stock one didn't have one. I'm very happy with it. Here's my pics:  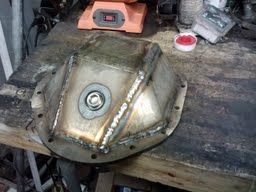 I welded mine up before all this talk about warping and stuff. I just laid mine out on a bench and went to town. Skipping around and letting it cool some. It may have a little warpage, but I put it on, drove it a little, and didn't get any leaks. I weleded the seems inside and outside.
|
|
|
Post by davidsyj on Apr 14, 2013 7:30:06 GMT -6
I did the same thing. I welded mine up on the table doing small stitches on opposite sides of the cover, cooling it down between welds. I did have to use my 4" DeWalt grinder to make enough clearance for the bolt heads to sit flat on the ring. And of course, in doing so, I got juuuuuuuuussssssstttttt deep enough into one of the welds where I had a pin hole. And of course, it was where the very bottom center bolt was..... So, I took my die grinder, removed the paint, got a rag, got a welder, kept tacking it until the leak stopped, then welded that spot up.
No other leaks and it fits and looks great. Very time consuming though but it was worth the "I welded that cover together" talk.
|
|
|
Post by TJNoe on Apr 16, 2013 11:55:25 GMT -6
I did the same thing. I welded mine up on the table doing small stitches on opposite sides of the cover, cooling it down between welds. I did have to use my 4" DeWalt grinder to make enough clearance for the bolt heads to sit flat on the ring. And of course, in doing so, I got juuuuuuuuussssssstttttt deep enough into one of the welds where I had a pin hole. And of course, it was where the very bottom center bolt was..... So, I took my die grinder, removed the paint, got a rag, got a welder, kept tacking it until the leak stopped, then welded that spot up. No other leaks and it fits and looks great. Very time consuming though but it was worth the "I welded that cover together" talk. Pics man!!!! PICS!!!!!!!!!!!!!
|
|